Additive Manufacturing
Additive Manufacturing
We are currently using additive manufacturing to speed up the new product development process—bringing products to faster with 2-3 week lead times. There are five major Additive Manufacturing (AM) processes we are currently using to create these short lead times.
Our suppliers are using 3D patternless technologies that are installed in the foundry—providing an in-house turnkey solution for the highest quality. The foundries we use that are deploying AM technologies understand the casting requirements for your industries and use these technologies alongside their standard foundry processes (green sand, no-bake etc.).
Scanning
Creating a 3D model is essential to the 3D patternless casting process. In order to use sand printing, Robomolding, metal printing, and PLA prints you need a good working model. Most companies have a 3D model available from the prototyping side of the business. On the aftermarket/legacy side of the business many companies have patterns they use once every three or five years for replacement parts. 3D scanning gives companies the ability to eliminate storage of these old patterns and scan them by creating fully functional 3D models. Scanning becomes an insurance policy as creating a 3D model can be difficult from 2D drawings as often revisions are not recorded).
Scanning Options
- Scan an old pattern to create a 3D model using a Creaform HandySCAN and solidification software
- Take a 2D drawing and convert it into a 3D model using solidification software which many companies use when making one-offs for legacy components
- If the component is available we offer the ability to do a dimensional overlay which gives the customer to visual of what the component says versus the 2D drawing
3D Sand Printing
Sand Printing is best used to make one-offs for the legacy and for product development because there is no need to invest in a pattern. From the 3D file we can deliver the component in 2-3 weeks from the day the 3D model is received. We use the 3D Sand Printer to create a core and mold from the resin sand. Since the printer is integrated inside the foundry we take the core and mold and pour the casting. This process is best used for castings up to 1200 lb. Alloys poured: Steel, Stainless, Duplexes, Inconel, Bronze, Gray and Ductile Iron
Robomolding
We use an ABB robot to mill out a mold, from a block of no-bake. The core is printed from a 3D sand printer and then poured in-house. Since the printer is integrated inside the foundry we take the core and mold and pour the casting. This process is best used for casting up to 2,000 lb in iron and aluminum. Alloys poured: Aluminum, Gray and Ductile Iron, and Stainless Steel
Digital Casting
The Digital casting process is proprietary technology for creating prototypes and one-off castings. Taking a PLA print and pour right into a flask allowing the hollow print to evaporate. This technology is similar to the lost foam process. Parts can be produced in 2-3 week lead times after receiving the 3D file. Alloys poured: Gray, Ductile, and Chrome Iron
Metal Printing
Metal printing is used to make prototypes for product development and one-offs for the aftermarket before investing in the hard tooling. Parts can be up to about 500 lb. Limited to no machining is required of these parts, and parts can be delivered in 2-3 weeks from receipt of the 3D file. ISO and ASO Certification.
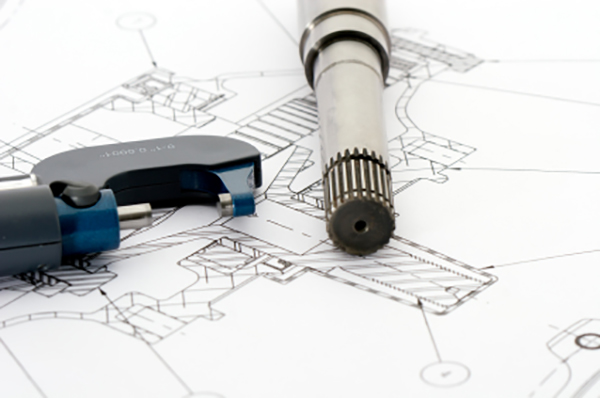